Welcome to Home and Auto Repair
At Home and Auto Repair, we offer top-notch handyman services for all your home and auto repair needs. With years of experience and a commitment to quality, you can trust us with your projects, big or small.
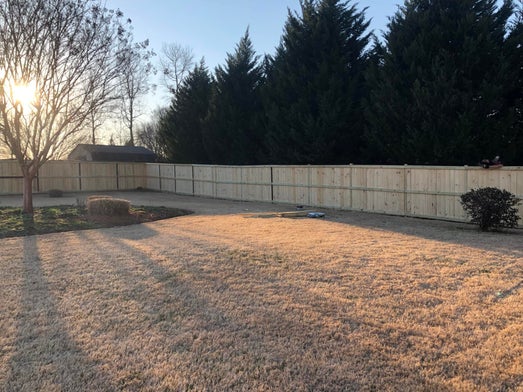
Services
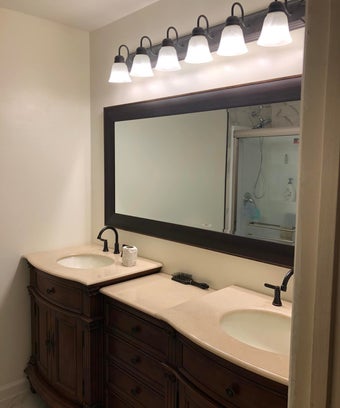
Home Repair
Comprehensive home repair and maintenance services with expert craftsmanship and attention to detail.
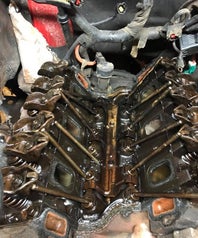
Auto Repair
Professional auto repair solutions for all your vehicle maintenance and repair needs.
Water Wells
maintainance and repairs
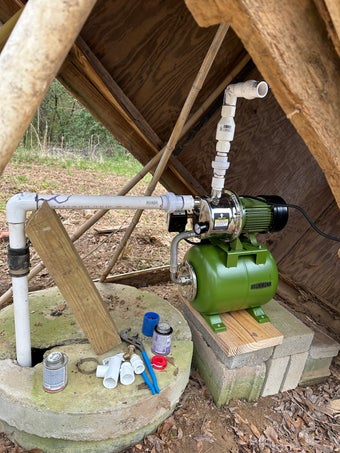
Maintenance Services
Regular maintenance services to keep your home and vehicle in excellent condition.
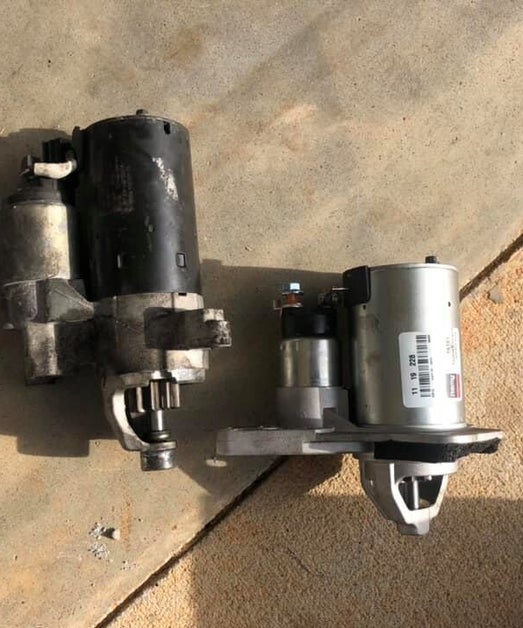
Frequently Asked Questions
“I was amazed by the professionalism and efficiency of Home and Auto Repair. They fixed my car and repaired a leaky faucet in no time. Highly recommend their services!”
— Sarah Johnson
Contact us
Contact us today for a free consultation and estimate!
Location
Home and Auto Repair
Spartanburg, South Carolina, United States
About us
At Home and Auto Repair, we take pride in offering professional and reliable handyman services to our clients. With a focus on customer satisfaction and quality workmanship, we are committed to delivering exceptional results for all your home and auto repair needs.